The Role of Maintenance in improving a company's competitiveness and profitability.
- Pedro Jose Barretto
- Dec 5, 2016
- 12 min read
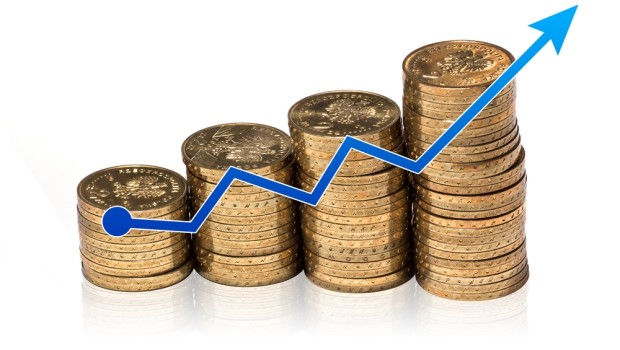
Maintenance plays an important role in bringing about improvement in company's competitiveness and profitability. Company's performance improves if areas generating core revenue are supported well and taken care of by undergoing continuous improvement and steady focus. Also maintenance has a major impact in the improvement of profitability in a company.
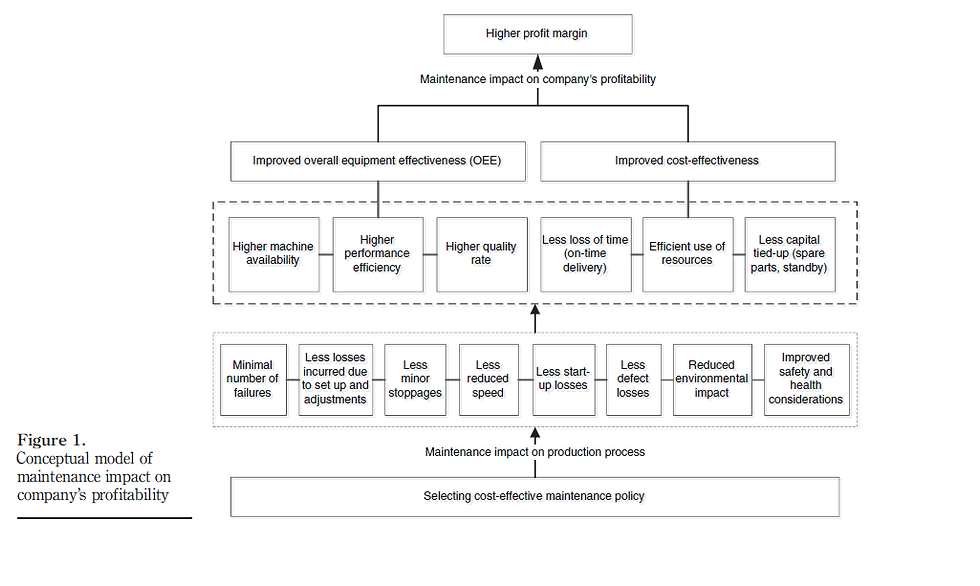
Based on the gap analysis done for a textile manufacturing plant as in picture

The results suggest that from respondents’ points of view, maintenance practices related to condition-based maintenance approach represent the highest opportunity for improvement. The most notable empirical results of the case study showed that around 3 per cent of additional profit could be generated at weaving machine, especially if all unplanned stoppages and loss of quality due to decrease in the productivity would be prevented.
This is just an example case study to understand how maintenance can improve the profitability of an industry as complex as a textile mill which you can see how complex the machines are.
The potential benefits of a maintenance policy provides productivity, quality and profitability to a company and that gives it a higher performance benefits based on a more effective maintenance policy.
Why a Maintenance policy ?
The economic downturn and the dynamic business environment drive companies to seek more efficient and effective maintenance (Van Horenbeek et al., 2010). Thus, the increasing competition in the market creates a need to search new ways in which companies can differentiate themselves and gain more profit and better competitive position. It is understood from Al-Najjar (2007) thesis a company’s internal effectiveness is strongly influenced by the maintenance role and impact on other working areas such as production, quality, production cost, working environment, amount of work in progress and tied up capital.
Effective maintenance is also critical to many operations. It extends equipment life, improves equipment availability and retains equipment in proper condition (Swanson, 2001). In general, it is not usual that old and deteriorated machines/processes can manufacture quality products with high overall equipment effectiveness (OEE) and at low prices (Al-Najjar, 1996). Thus, high equipment availability and high performance can be achieved through efficient equipment management programmes (Raouf and Ben-Daya, 1995). On contrarydisturbances in production processes due to maintenance and other causes reduce productivity; increase product cost and thereby reduces profitability (Alsyouf, 2007; Cholasuke et al., 2004). Applying effective maintenance aims to enhance company’s profitability and competitiveness through continuous costeffective improvement of production process efficiency, effectiveness and productivity, which can be achieved via maintaining and improving the quality of all the elements contribute in the production process continuously and cost-effectively (Al-Najjar, 2007).
The Theory

Maintenance approaches - A maintenance strategy involves the identification, researching and execution of many repair, replace and inspect decisions (Kelly, 1997). A maintenance concept can be defined as the set of various maintenance interventions (corrective, preventive, condition based, etc.) and the general structure in which these interventions are foreseen (Pintelon and Waeyenbergh, 1999). Several maintenance approaches, i.e. strategies and concepts, have been developed and implemented through the evolution of maintenance. The maintenance has emerged from failure-based maintenance, and has moved towards preventive and is now realized in the essence of process-oriented “holistic” approach (Alsyouf, 2007). Likewise, Waeyenbergh and Pintelon (2002) argued that maintenance has shifted from failure-based towards condition-based maintenance (CBM).
The relationship between quality, productivity and maintenance-
Much has beenwritten in quality management literature considering quality. For instance, Flynn et al. (1994) define quality management as an integrated approach to achieving and sustaining high-quality output. Several studies have also investigated the link between quality performance and cost reduction. For example, Maani et al. (1994) showed that quality performance (in terms of scrap, rework and customer complaints) has impact on operational variables (i.e. production cost, on-time delivery, worker idle time, lead time, productivity), as well as impact on business performance. However, interactions between quality and production can be also interpreted from maintenance point of view. The primary output of production is the desired product and its secondary output is demand for maintenance, which is in turn an input for the maintenance function (Ben-Daya and Duffuaa, 1995). Hence, a strong maintenance program is needed to provide reliable equipment maintenance and reduce equipment process variation (McKone et al., 2001). Therefore, maintenance major role should be maintaining the quality of the elements involved in production instead of just jumping from one repair to another, according to Al-Najjar (2007). Also, it affects production by increasing production capacity and controlling the quality and quantity of output.When outlining the link between quality and maintenance, it is also necessary to indicate that product quality, production cost, machine condition and its life length are not just influenced by the type of production machinery and maintenance policy, but also by the quality of the input of elements (such as raw material, production tools, methods and procedures, operating and maintenance staff competence and operating conditions) in the production process (Al-Najjar, 2007).
Maintenance impact on company’s profitability: a conceptual model
Maintenance is often regarded as a cost driving necessity rather than a competitive resource, especially within the manufacturing industry. A survey performed by Alsyouf (2004),showed that 70% of the respondents considered maintenance as a costcentre. However, in many studies (Al-Najjar, 2000; Mitchell etal.,2002; Waeyenberghand Pintelon, 2002) authors have emphasised the role of maintenance in improving performance and profitability of manufacturing processes. This suggests that maintenance is no longer a cost centre, but could be profit-generating. In general, improvements in the performance of a maintenance policy aim to reduce production cost and increase company’s profit and competitiveness through enhancing process availability, performance efficiency and quality rate (Al-Najjar, 2007). In this regard, we present a model (Figure 1) at the start of the article that describes the interaction between maintenance, production and company’s profitability.
The model illustrates how an effective and efficient maintenance policy could affect the production process by improving OEE and cost-effectiveness.Thus, considering these elements company could benefit in higher productivity and nevertheless in higher profit margin. Moreover, it is essential for companies to apply different indicators in order to assess and monitor the influence of the selected maintenance policy on production performance and consequently on the company’s business. Different measures can be taken into account to assess the financial impact of maintenance on company’s business (see Al-Najjar, 2007; Alsyouf, 2007). Nevertheless, it is also important to apply different indicators, such as maintainability indicators (Moreu De Leon et al., 2012) as well as safety, security and environment (HSSE) indicators (Parida and Chattopadhyay, 2007), aiming to provide the required information to the management for effective decision making (Parida, 2007). Several different tools and technique such as failure mode effects and criticality analysis and reliability, availability, maintainability and safety analysis can also be viewed as a support to the decision-making process, which ultimatelycan affect the company business (Gonzalez-Prida and Crespo Marquez, 2012).
Research methods - Gap Analysis - By identifying the gaps in a company, it is possible to discover areas where company needs to put more attention.In terms of improvement efforts. The idea behind this gap analysis is to ask the respondents both about agreement (P) and importance (I) of different maintenance practices.
Generally the importance (I) means the respondents needs and the agreement ( P ) means company’s performance.
Profitability and quality analysis- The term profitability is the overriding goal for the success and growth of any business; it can be defined as the ratio between revenue and cost (Tangen, 2005).In order to address the purpose of this study we followed the approach of Alsyouf (2007), which can be discussed with American Productivity Centre (APC) model. APC model is based on the premise that a firm generates profits from two sources, productivity and/or price recovery improvements (Rao, 2000). Profit-linked total-factor productivity measurement models are well established in organizational performance measurement. Two of the established profit-linked total-factor productivity measurement models are the aforementioned APC model (Rao, 2000) and the PPP (profitability¼productivityþprice recovery) model (Miller, 1984). The advantage of total-factor measurement models lies in the fact that they link productivity to profitability (Miller, 1984; Miller and Rao, 1989; Sink et al., 1984). In this study we focused on productivity, since it is hard to trace the changes in the price recovery index (Alsyouf, 2007). This approach also considers that for a given period of time, the variable cost (e.g. the cost of raw material per item), can be considered constant. On the other hand, the fixed cost per unit quality item will decrease based on how many items were produced in that period (Alsyouf, 2007). Therefore, company’s profit in relation to productivity, can be calculated by using:
Profit before improvement F1 = Q1 (Price-TC1) ---- 1
Profit after improvement F2 = Q2 (Price-TC2) ----- 2
NetProfit = F2-F1
Using these formulas, author assumes that Q1 is the quantity of quality product produced when using a certain maintenance policy, which resulted in total manufacturing cost (TC1). However, if company improves the effectiveness of the implemented maintenance policy,or uses more effective maintenance policy that requires a new investment of (I) this could result in increasing the quantity (Q2) and consequently in new TC2. If the net profit is greater than the cost of improvement, i.e. I, required for achieving the increase in output, then the investment is cost effective (Alsyouf, 2007).
Quality can be defined as the degree to which a company meets customers’ perceptions on a variety of characteristics of the delivered products/services, and is often expressed and managed using a variety of technical quality factors such as percentage of defect goods (Slack et al., 1998). The quality rate can be used to indicate the proportion of defective production to the total productive volume (Dal et al., 2000). Thus, quality rate can be calculated as the ratio of good quantity produced to the sum of total produced quantity, by using:
Q=Quality rate=(Total production(units)-Defect amount(units)/Total production(units)
From the performance of the Textile manufacturing company comprising of 8 machines

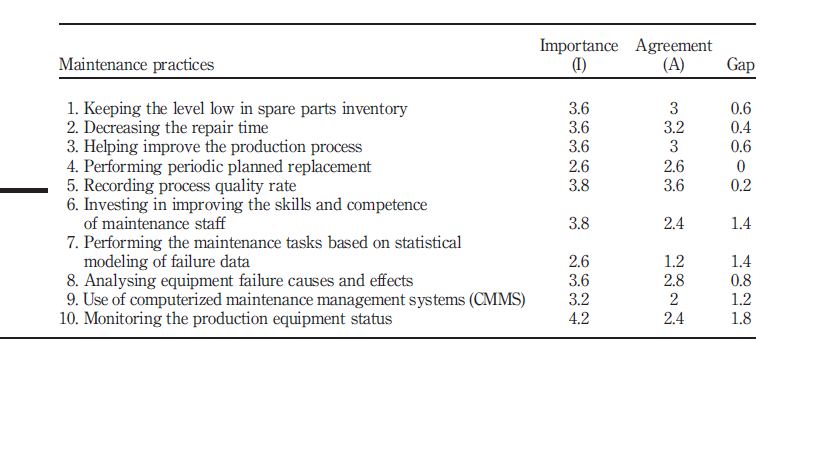
According to the conceptual model presented in this paper it is essential for companies to implement cost-effective maintenance policy in order to enhance their profitability. Nevertheless, it was found in many cases that an efficient CBM influences company’s profit and competitiveness (see for instance Al-Najjar, 2007). In addition, Ilangkumaran and Kumanan (2009) stressed the importance of selecting a proper maintenance policy in the textile industry. The aim of the second phase of this case study was to exemplify the benefits that company could gain in terms of productivity and profitability of a manufacturing process, if more effective maintenance policy would be implemented. In this section we also discuss the maintenance impact on product quality. For this purpose the case study involved analysis of technical and economic data. First, the data analysis involved the identification and analysis offactors that cause the stoppage time. Based on the received data, the total stoppage time was distributed as short stoppages 60 per cent, unplanned stoppages 30 per cent and regular planned stoppages 10 per cent (Figure 3). The short stoppage constitutes the largest portion of the stoppage time. Some stoppages were planned in order to perform maintenance tasks. It was estimated that 60 per cent of time spent for maintenance effort for this machine is for planning activities. However, according to the results 10 per cent of total stoppage time belongs to planned stoppages. Thus, this represents opportunity for improvement, by implementing more efficient and effective maintenance policy.
The main causes for unplanned stoppages were due to electrical reasons, sewing threads, start-ups and adjustments of machine. Therefore, all these unplanned stoppages affect the productivity and quality, and by minimizing them, companycould benefit in higher profit margin, as we presented in the conceptual model (Figure 1). Hence, in study (Al-Najjar and Alsyouf, 2004) authors found that on average a value of around 3.5 per cent of the actual generated profit could have been gained if, ideally, all the failures, had been avoided using an efficient maintenance policy. For calculating company’s profit we used economic data and data relating to productivity. Machine’s average monthly quantity produced was Q1=5,280 items and the total production were 5,500 items per month. The average selling price was about 10.60€ per item. The average TC1, at Q1 was 7.55€ per item. The average quantity of production lost due to all types of unplanned stoppages was estimated about 88 items per month. In ideal case, if an effective maintenance policy would eliminate all stoppages, the new quantity produced would be 5,368 items per month, and TC2 would become 7.50€. Thus, the impact on the company profit, considering improved productivity (without the considering any other costs, for instance cost of investment) was calculated by using Equations (1)-(3):
Profit before improvement F1= Q1(Price-TC1)=5,280(10.60€- 7.55€)=16,104€ Profit before improvement F2 = Q2(Price-TC2)=5,368(10.60€- 7.50€)=16,640.8€ NetProfit= F2-F1 =16,640.8€ - 16,104€ = 536:8€
This means that in ideal case around 3 per cent of the profit per month could be additionally generated at weaving machine, according to improved productivity at one weaving machine. However, this result represents just the impact of productivity on company’sprofit.Therecouldbeseveralothersfactors,suchaslessconsumedspareparts, less tied up capital in inventory, less delivery delay penalties and lower maintenance cost, that could influence the production process and therefore affect the manufacturing costs. This calculation does not include economic losses, such as, for example the cost of an idle machine in the time when the machine is not producing due to failures.The empirical data showed that quality rate according to Equation (4) was 96 per cent. The results also showed that by using an efficient maintenance policy, company could increase quality rate in an ideal case for around 1.5 per cent. The value for quality improvement was estimated according to the company personnel’s experience, regarding the production lost due to causes related to maintenance problems. Additionally, we assume that quality rate could be improved even more, if causes of failures due to operator’s mistakes would be minimized. Higher knowledge and involvement of operators could improve equipment performance. In this regard, Crespo Marquez et al. (2009) suggest that higher levels of knowledge, experience and training is required, and at the same time, techniques covering the involvement of operators in performing simple maintenance tasks are extremely important to reach higherlevels of maintenance quality and OEE. As such, it is also important for managers to support continuous improvement activities in order to improve maintenance performance (Maletic ˇ et al., 2009, 2012). The findings represent the economic result of an effective maintenance due to its impact on productivity and profitability of a manufacturing process. According to Khan and Darrab (2010) a good maintenance policy and strategy leads towards improving equipment reliability and maintainability, maximizing OEE and acts as contributor to quality and to higher productivity. An influence of an effective maintenance policy on productivity and profitability was also proved by empirical studies (Alsyouf, 2007; Al-Najjar, 2007). Hence, our results directly support the study of Alsyouf (2007) by providing the evidence of maintenance impact on productivity and consequently on company’s business. However, our results also support the view of different studies (e.g. Swanson, 2001), which suggest that proper maintenance could ensure smooth running of machinery and uninterrupted flow of processes, which consequently leads to higher productivity, as well as better product quality. Hence, improving quality positively enhances operational performance and productivity, and certain indicators of business performance (Maani et al., 1994).
While empirical findings provide interesting insight into maintenance in relation to the company’s quality and profitability, this can be also discussed in the view of the current state of the maintenance activities in the company. Maintenance function is organized as a part of production department. It is found that time spent for planning does not result in preventing the failures in desired level, in order to reduce the level of unplanned stoppages. Further analysis reveals that company is not using advanced maintenance approaches and that there is still high portion of corrective maintenance. The main tasks conducted considering maintenance are, for instance: restoring equipment to operation, installing new equipment, etc. On the other hand some activities are focused in production process, such as, for example, helping improve the production process. Therefore, company is aware of the role of maintenance, but need to set maintenance strategy in order to be successful. However, this brief observation can be discussed in the view of our empirical results. If company would put more effort in implementation of modern maintenance approaches, such as CBM for properly describing current machine condition and predicting its future status it could prevent and minimize unplanned stoppages, and therefore benefit from higher quality and productivity.
Results
Our study underscores the previous assertions that company can benefit from implementing more efficient maintenance policy (Lo ¨fsten, 1999; Al-Najjar and Alsyouf, 2004; Al-Najjar, 2007). Also consistent with prior studies (e.g. Al-Najjar, 2007) are the interactions we found (Figure 1) between maintenance, production and company’s profitability. As presented in the proposed conceptual model a company could also benefit in terms of reducing environmental impact and improving safety and health aspects, especially if more efficient maintenance policy would be implemented. This implies that maintenance is endorsed by complex interactions with working areas such as production, quality, personnel competence, operating environment, etc. (Al-Najjar, 2007). This brings up new opportunities for a future research, mainly in terms of investigating the interactions between maintenance and these areas in more depth. Management often looks at maintenance as a necessary evil, not as a mean to reduce costs (Paz and Leigh, 1994), or as a potential profit generating function (Al-Najjar, 2007). However, in today’s highly competitive environment manufacturing systems are struggling to operate more effectively (Oke, 2005). This means that it is necessary to implement a proper maintenance policy in order to remain competitive. Thus, by assessing potential benefits company could reveal how cost-effective the investments in maintenance were and whether or not they were relevant (Al-Najjar and Alsyouf, 2004). Maintenance should be viewed as a value-adding activity. From theoretical point of view this study therefore demonstrates that maintenance should be treated as a profit generating function. The main implication for managers that has emerged from the study is that managers in manufacturing companies should place emphasis on assessing and monitoring the impact of maintenance on company’s business. Therefore, managers could identify the potential benefits of maintenance policy in terms of productivity, quality and profitability.
This study has been taken from - Journal of Manufacturing Technology Management ISSN 1741-038X Volume 25 Number 4 2014
Comments