PLC & DCS maintenance Plan & Reliability
- Pedro Jose Barretto
- Nov 28, 2016
- 5 min read
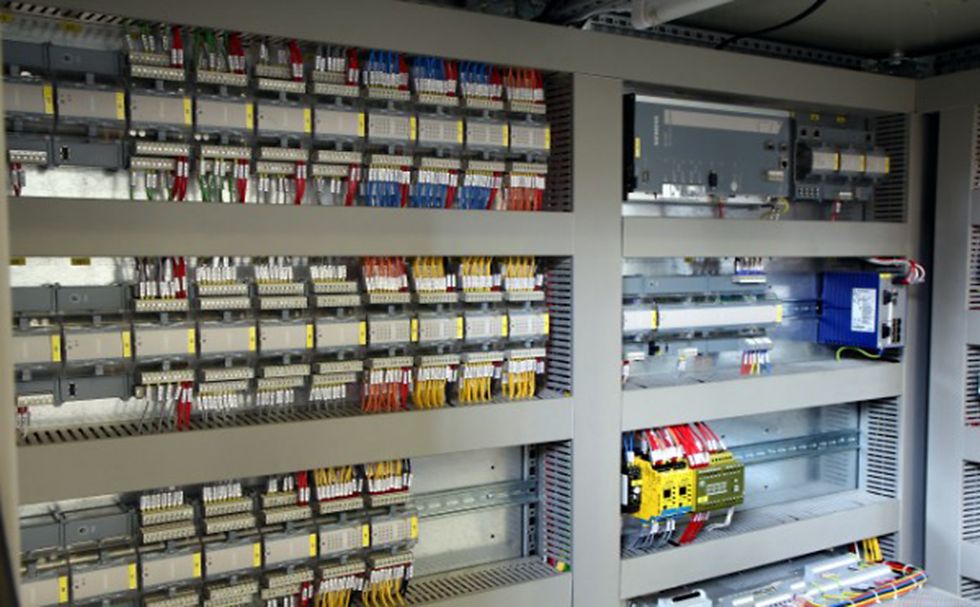
With the advancement of PLC & DCS systems in continuous process industries and the availability of advanced inbuilt diagnostic functions available in the system it is expected that failures should not occur and the systems currently are 100% reliable. This is ideally not true. Since plant production is so much dependent on the optimal performance of the system, the question of expectation of failures is unexpected looking into the high level of engineering involved in production of the PLC & DCS systems themselves. Experience led results show a different picture that failures do occur which cause a big problem for companies production availability. I beleive as per the current architectures of commonly available PLC and DCS system brands the technologies available are scalable and its a one time investment for process plants as the technology available is scalable. But we still have failures and one does not know how to draw a line and where to draw it.
Therefore the debates and issues faced by process industries using popular brands of PLC and DCS are:-
1. How many spare electronic cards have to be kept to keep the system running? Should the OEM keep the spares ? Will the spare be available immediately at the time of failure? At what cost it would be available? If the spare is procured to be stored within the company will it work when it is required? Do we need to have an AMC with OEM?
2. Will the application software SCADA and DCS be reliable in the long run? Should Capital expenditure planning be done for software? This issue is rarely a big issue as today popular PLC & DCS OEM providers in order to keep their software marketable develop some inbuilt diagnostic tools with an approach to induce industrial users of their DCS & SCADA system to purchase so as to keep their software buisness in motion. Experience has shown that its not a good idea to invest in new DCS & SCADA software unless the hardware is changed.
All the above issues involve a lot of money investment which continuously tasks the mind of maintenance engineers to convince operational heads for budgetary approvals for upgrades or functional improvement in the system for use in the process. In view of criticality of process the budgets are approved and executed to prevent a loss in availability but does such investment helps? is such cost required? is there a way we can proactively measure and prevent failures of a running system and then take corrective measures which will prevent failures and give good sleep to operation managers and operation personnel including maintenance engineers and technicians . All answers come down to implementing a good Maintenance approach.

To refresh ourselves about Maintenance - it is a set of actions done with an objective to keep an item in its fully functional state. This can be divided into types like
Breakdown Maintenance - which is a repair action carried out only when an item breaks or fails,
Preventive Maintenance - which is an a activity carried out to keep an item functional and is split into
Periodic Maintenance - based on absolute time
Predictive Maintenance - based on actual working conditions ,
Corrective Maintenance - are actions involved which improve equipment with design issues to improve its functionality and
Maintenance Prevention - which are actions performed to reduce maintenance requirements based on past experience with similar equipment.
So in order to keep our PLC's and DCS systems optimum we need to carry out the first two.
Which will restore full functionality every time a certain type of failure is detected by the system itself.
Regularly inspect the system, and re‐establish the full functionality in case the inspection shows some performance decrease.
using the concept of RCM ( Reliability Centred Maintenance ) approach we apply an optimal balance between lower activity cost and higher equipment reliability.
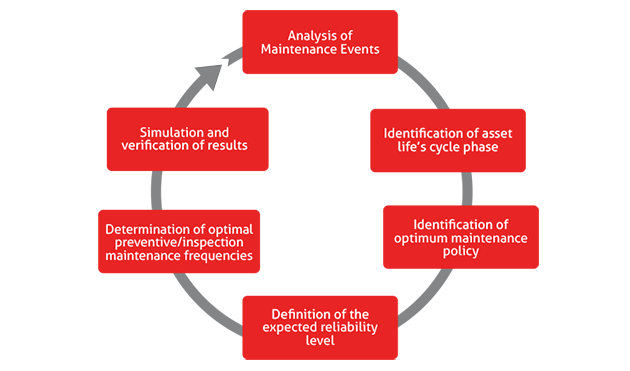
The technical standard SAE JA 1011 “Evaluation Criteria for RCM Processes” sets the criteria to implement Reliability Centered Maintenance. It is based on the questions here below, to be answered in the given sequence:
1. What is the item supposed to do and its associated performance standards?
2. In what ways can it fail to provide the required functions?
3. What are the events that cause each failure?
4. What happens when each failure occurs?
5. In what way does each failure matter?
6. What systematic task can be performed proactively to prevent, or to decrease the consequences of the failure?
7. What should be done if a suitable proactive task cannot be found?
The above questions give a lot of answers to us and make us understand that we need to chalk out the following
A good maintenance Plan to improve reliability - We sometimes think that PLC and DCS are static devices and reliable themselves but since they are logic devices they are subject to changes in their working conditions which may breach functionality. How ? Suppose the automation system looks after a safety function like a pressure protection system logic. This function can be checked only when we have a maintenance plan which will document and check the functionality of the Logic. Since this will be a dynamic condition the metric to be considered is the probability of failure on demand (PFD) which is a value that indicates the probability of the system failing in response to a demand. ( which in our case is when the logic condition occurs ) . Hence maintenance plan of the automation system has to be based on how critical is the process it looks after.
Knowledge of the failure rates- Knowledge of PLC/DCS OEM manufacture failure rates using IEC61508 manufacturer declaration should allow us to estimate the “ideal” failure rate of the equipment in use.
Knowledge of causes of failures - Knowledge of failure rates applies if we assume all conditions are perfect around the boundaries of the components but then we have to consider - Ambient cabinet temperatures at the tolerable levels, Ambient temperature oscillations,Moisture, Dust, Corrosion, Electromagnetic interference,Power supply stability,Vibrations ,Age in condensors, transformers and die electric materials, Grounding and earthing separate from plant equipment,Neutral to Earth voltage less than 1 Volt, Induced currents due to routing of power cables close to electronic cables, Occurance of welding or high current drawing activity near Cabinet.I/O short circuits i.e no isolation of the I/O cards from external shorts, Wildlife activity like rodents and rats , Design problems ,Maintenance issues like - mistakes, distractions, underestimated impact on other equipment, missing or wrong documentation,Human unauthorised access,Bad housekeeping near the panels

To ensure trouble free performance a preventive maintenance plan could be made assuming FAT, SAT and Commissioning tests are completed.
Periodical maintenance during plant operation: it will include all checks that can be safely done during plant operation, and all checks which MUST be done only during operation.
Periodical maintenance during plant shut down - It must be the checks that need to be done when plant is shutdown.
Periodical Proof test: it is normally required for SIS protective equipment. The Proof Test procedure should clearly define the associated plant conditions: in operation or shut‐down.
Sility
Comments